II. Development of Cementless Structural Binder for Construction Purpose
using Industrial Waste By-product Materials.
2.1. Sustainable Problems in the use of Portland Cement
According to European Union (EU), half of materials obtained from the Earth surface are used for construction and its construction waste is responsible for more than 25% of total wastes generated in Europe every year; however, this example ironically suggests that sustainable development can be significantly accomplished by the construction sector with efforts of reducing excessive consumption of natural resources and lowering harmful wastes.
2.2. Solutions for The Problems
To resolve such problems of Portland cement, two possible ways may be suggested:
1. Use of cementless binders (e.g., geopolymer, CaO-activated slag) for concrete production
2. Conducting nano-/micro-structural studies on concrete

2.2.1 What are cementless binders?
Cementless binders are emerging materials to replace Portland cement in concrete production. These are generally produced by alkaline activation of reactive aluminosilicate materials. Cementless binders have gained great interest from various academic fields such as waste management, mineral, hazardous materials, environments, chemistry, applied sciences, and structural engineering, etc. as well as industries, not only because these can completely replace Portland cement in construction with providing various environmental engineering properties (e.g., immobilization of heavy elements in contaminated soils or water), but also they can be made using only industrial waste by-products such as coal fly ash from power plant, blast furnace slag from iron-manufacturing, or red mud from Al-manufacturing.
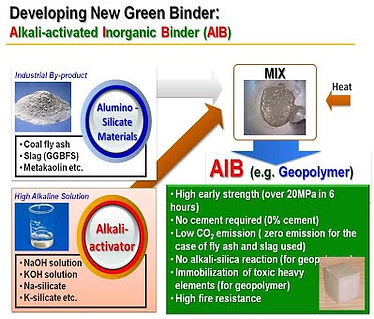
(Figure) Schematic process of
non-cement binders production
2.2.2 Possible Raw Materials for Cementless Binders
Candidate Material #1: FLY ASH
Fly ash is a waste by-product of coal-based power plants. Recycling of fly ash has been extensively studied in science and engineering fields mainly because a huge amount of fly ashes are still deposed in nature although cement and concrete manufacturing industries are increasing to consume it. Currently, a world-wide annual production of fly ash is estimated about 2 billion tons; however, only less than 50% is being recycled. According to the American Coal Ash Association (ACAA), in 2004, 70.8 million tons of fly ash was produced in U.S., but 42.7 million tons of coal fly ash was disposed in landfills or sea; in Europe (EU 15), in 2007, 41 million tons of fly ash was generated, but the utilization rate was only 47%. Thus, the recycling of fly ash is now being one of top environmental and economical issues. Note that fly ashes contain quite large amount of leachable toxic heavy elements such as Ag, Hg, Cr, Cd, Pb and Zn etc., and thus the disposal may lethally contaminate soils and sea.

(Figure) Typical dumping site of coal fly ash next to coal-power plant (taken from Google image)

(Figure) Coal fly ash (taken from Google image)
Candidate Material #2 : Red mud
The red mud is a residue of alumina-manufacturing process, known as the Bayer process. 70 million tones of red mud is being globally produced every year, and its disposal remains an issue of great importance with respect to environment. The red mud has a slurry form possessing high pH (=~13) solution, which make it very toxic. In October 4, 2010, in Ajka, western Hungary, one of red mud reservoirs in Al-manufacturing plant burst and 35 million cubic meters of the red mud flooded into three villages; 9 people died and over 150 people were hospitalized. Although the red mud has been under research for recycling, there has been no clear solution for it. Geopolymer production using red mud has a great potential.

(Figure) Disaster of burst spill of red mud dumping reservoir in Hungary at 2010. Million gallons of caustic red sludge was spilled into near villages and 10 people were died. The toxic red med flowed into drinking water source (e.g., Danube river) in Europe. The deposition of red mud itself is very dangerous and thus should be recycled by cementless binder production (taken from Google image)
Candidate Material #3 : Granulated blast furnace slag
Granulated blast furnace slag (hereafter, called slag) is a waste by-product of steel industry. Slag is formed through a metallurgical smelting process when iron ore, coke and flux (e.g., limestone) are mixed and melted together in a blast furnace. The worldwide annual production of slag is over 330 million tons (e.g., 15 million tons in U.S., 23.5 million tons in Europe, 200 million tons in China, 30 million tons in Japan, 12 million tons in South Korea in 2010). Currently, about 60% of the slag is annually recycled, but the remaining of 40% of this slag is being dumped into the Earth. This disposal rate requires more intensive research works to reduce the rate. Slag can be converted to a binding material for construction by alkali-activation technologies, which do not need any use of Portland cement. Note that although alkali-activation of slag is quite similar to geopolymer, the reaction products of alkali-activated slag are distinctly different from those of geopolymeroc reaction from fly ash, red mud and metakaolin. The major reaction product of alkali-activation of slag is calcium silicate hydrate (I) (= C-S-H (I)), which is very similar to cement hydration product, C-S-H, but a main product of geopolymer is an aluminosilicate gel (also called geopolymer), which is similar to zeolites (e.g., hydroxysodalite, hydroxycancrinite, chabazite).

(Figure) The process of producing iron in steelworks (taken from Google)

(Figure) ground granulated blast furnace slag (taken from Google)
Candidate Material #4 : Stone powder sludge
Stone powder sludge is a by-product of coarse aggregate manufacturing of construction industry and is being annually generated 7.5 million tons in South Korea. Currently, most stone powder sludge is just disposed in landfills in Korea because there is no particular way of recycling. The chemical composition of stone powder sludge is quite similar to that of fly ash and metakaoline, which have high proportion of alumina and silica, but this material does not contain any glass phase, which makes a very low degree of chemical reactivity. Nonetheless, this material should be recycled.